Table of Contents
- Introduction
- Common NDT Techniques Used in Aerospace
- Benefits of NDT in Aerospace
- Real-World Examples
- Why Safety is Paramount in the Aerospace Industry?
- Conclusion
Introduction
In the vast realm of aerospace engineering, safety stands as an unyielding cornerstone. The importance of ensuring reliability and Non-Destructive Testing (NDT) solutions for the aerospace industry.
As you navigate through this interactive journey, you’ll discover how NDT techniques contribute to the maintenance of aircraft integrity, the prevention of accidents, and the advancement of aerospace safety standards. From detecting hidden flaws in critical components to embracing emerging technologies, we’ll explore how NDT continues to shape the future of aerospace engineering.
Common NDT Techniques Used in Aerospace
Common NDT techniques used in aerospace include industrial NDT like ultrasonic testing, eddy current testing, radiographic testing, and magnetic particle testing. These techniques allow for thorough inspection of critical aircraft components to detect any abnormalities that could compromise safety or reliability. Here’s a detailed breakdown of common non-destructive testing techniques used in aerospace, along with their applications and examples.
Visual Inspection
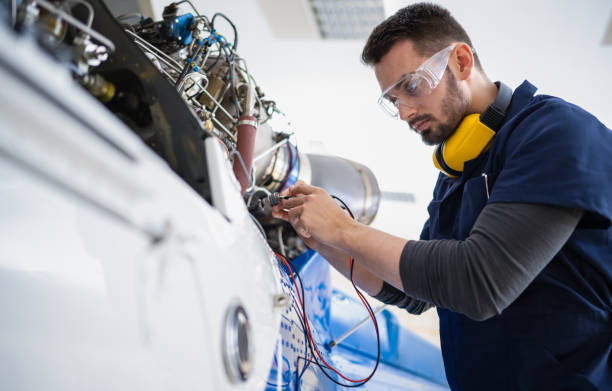
Visual inspection stands as one of the oldest yet most essential methods for evaluating aerospace components. This technique involves a direct examination of surfaces, enabling inspectors to identify visible defects, irregularities, or signs of damage.
Application: Visual inspection plays a pivotal role in assessing the surface integrity of aerospace components. By visually examining critical parts such as aircraft fuselages, professionals can detect indications of corrosion, rust spots, or paint damage, ensuring the structural integrity and safety of the aircraft.
Example: In the context of aircraft maintenance, visual inspection entails scrutinizing the fuselage for any signs of corrosion, including rust spots or paint deterioration. Detecting such issues early on allows for timely maintenance interventions, preventing potential structural compromises, and ensuring the airworthiness of the aircraft.
Ultrasonic Testing (UT)

Ultrasonic testing (UT) represents a sophisticated non-destructive evaluation technique widely employed in the aerospace industry. UT uses high-frequency sound waves to penetrate materials, revealing internal flaws or defects that may compromise structural integrity.
Application: UT serves as a vital tool for inspecting aerospace materials, particularly for detecting internal defects hidden beneath surfaces. This method is commonly used to assess critical components, such as aircraft engine parts, for cracks, voids, or other imperfections that could impact performance and safety.
Example: When examining aircraft engine components like turbine blades, ultrasonic testing is used to probe beneath the surface for any internal flaws. By detecting minute cracks or voids that may not be visible to the naked eye, UT ensures the reliability and functionality of essential aircraft systems.
Radiographic Testing (RT)
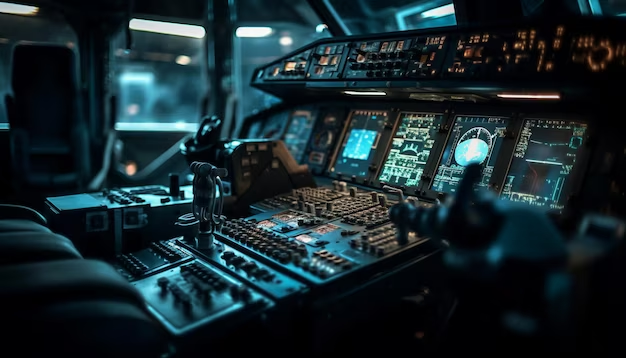
Radiographic testing (RT) represents a sophisticated non-destructive evaluation method employed to inspect the internal structures of aerospace components. By utilising X-rays or gamma rays, RT can penetrate materials, producing detailed images that reveal hidden defects.
Application: RT is indispensable for assessing the integrity of critical aerospace structures, allowing inspectors to identify internal flaws or defects that may compromise performance or safety. This method is commonly used for inspecting welds in aircraft structures for indications of incomplete fusion or porosity.
Example: In the inspection of welded joints in aircraft structures, radiographic testing is employed to examine the internal integrity of the welds. By producing detailed images of the welds’ internal structure, RT enables inspectors to detect any hidden defects that could weaken the joint and jeopardise the aircraft’s structural integrity.
Eddy Current Testing (ET)
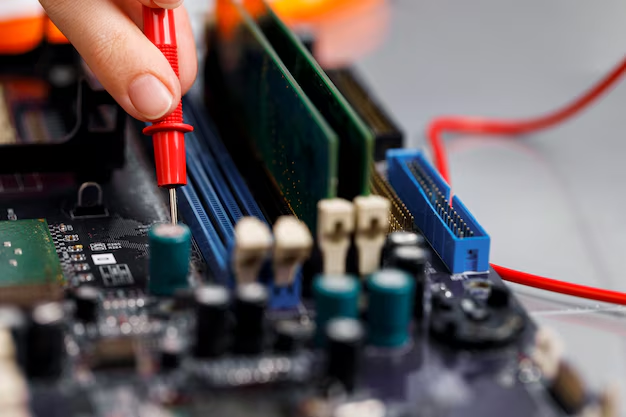
Eddy current testing (ET) is a non-destructive inspection technique based on electromagnetic principles, widely utilised in the aerospace industry. ET detects surface and near-surface defects in conductive materials by inducing electromagnetic fields.
Application: ET is particularly effective for screening aerospace components for surface irregularities or defects, offering high sensitivity and accuracy. This method is commonly employed to inspect aircraft fuselages for indications of fatigue cracks or material thickness variations.
Example: When screening aircraft fuselage for surface cracks or variations in material thickness, eddy current testing is utilised to detect any hidden defects. By inducing electromagnetic fields and analyzing resulting impedance changes, ET enables inspectors to identify potential issues that may compromise structural integrity.
Magnetic Particle Testing (MT)
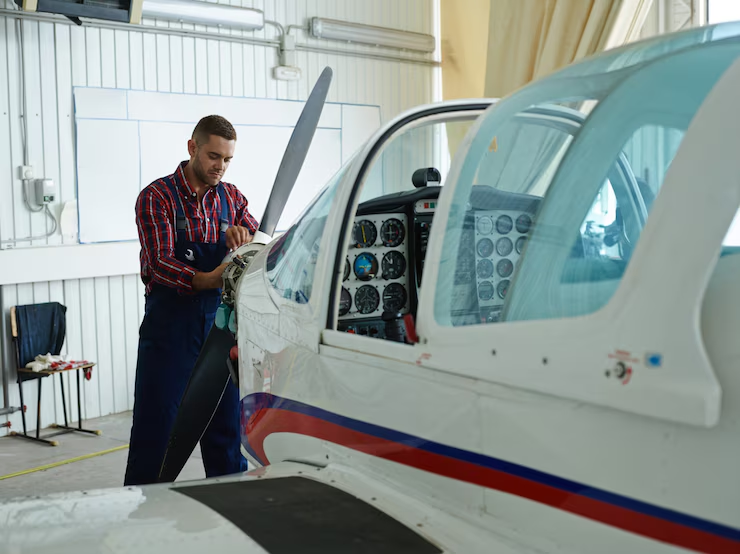
Magnetic particle testing (MT) is a widely used non-destructive evaluation method for inspecting ferromagnetic materials in the aerospace industry. MT detects surface and near-surface defects by applying magnetic particles to the material’s surface.
Application: MT is essential for identifying surface defects in critical aerospace components, ensuring their reliability and safety. This method is commonly used for inspecting aircraft landing gear components for indications of surface cracks or defects that could compromise performance.
Example: In the inspection of aircraft landing gear components, magnetic particle testing is employed to detect any surface cracks or defects. By applying magnetic particles to the surface and observing their behaviour under magnetic fields, MT enables inspectors to identify potential flaws that may necessitate corrective action.
Liquid Penetrant Testing (PT)
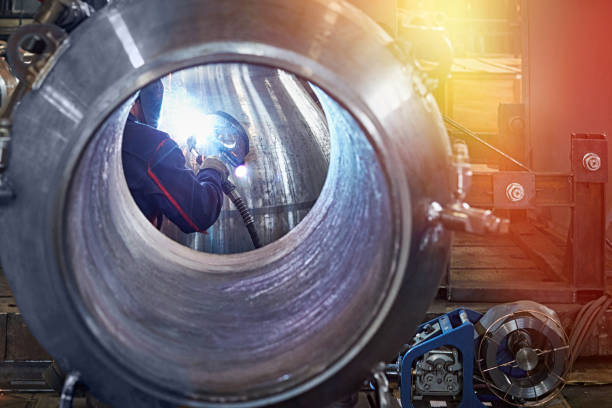
Liquid penetrant testing (PT) is a versatile non-destructive inspection technique used to detect surface-breaking defects in aerospace materials. PT involves applying a liquid penetrant to the surface, which seeps into discontinuities, revealing hidden flaws upon developer application.
Application: PT is widely employed in the aerospace industry for inspecting critical components with smooth or non-porous surfaces. This method is effective for identifying surface cracks, flaws, or discontinuities that may compromise the integrity of aerospace structures.
Example: When examining aircraft engine components such as turbine discs, liquid penetrant testing is utilised to detect surface cracks or flaws. By applying a penetrant solution and observing any indications of leakage, PT enables inspectors to identify potential defects and prevent catastrophic failures during operation.
Thermography
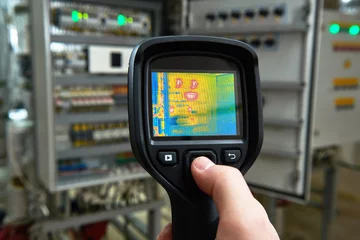
Thermography represents an advanced non-destructive inspection technique used to detect variations in temperature across the surface of aerospace structures. By utilising infrared imaging, thermography can identify subsurface defects or delaminations.
Application: Thermography is particularly valuable for inspecting composite materials used in aerospace structures, where traditional inspection methods may be inadequate. This method enables inspectors to identify hidden defects or damage by analysing temperature variations across the surface.
Example: In the inspection of composite aircraft structures, thermography is employed to detect any hidden defects or delaminations. By capturing infrared images and analysing temperature variations, thermography enables inspectors to identify areas of concern and take appropriate corrective actions.
Acoustic Emission Testing (AE)
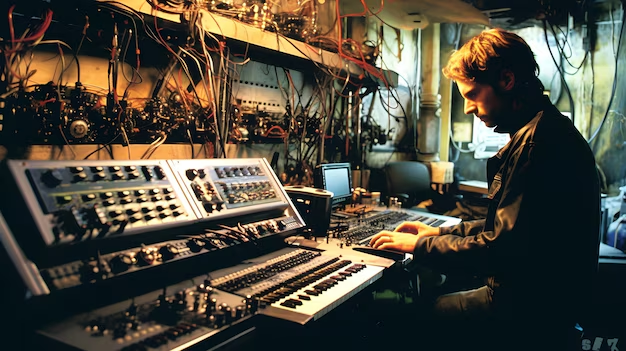
Acoustic emission testing (AE) is a dynamic, non-destructive inspection method used to monitor the release of stress waves or acoustic emissions from materials. AE helps detect active defects or damage in aerospace structures during operation.
Application: AE is crucial for monitoring the structural health of aerospace components, particularly during flight operations. This method enables inspectors to identify indications of crack propagation, structural degradation, or other active defects that may compromise safety.
Example: When monitoring aircraft wing structures for crack propagation or structural degradation, acoustic emission testing is employed. By detecting stress waves or acoustic emissions emitted by active defects, AE enables inspectors to assess the structural integrity of aerospace components and ensure safe operations.
These NDT techniques are essential for maintaining the safety, reliability, and airworthiness of aerospace components and structures by enabling non-invasive inspection and early detection of defects.
Whether you’re seeking ultrasonic testing equipment, magnetic particle inspection tools, or radiographic testing accessories, we’ve got you covered with precision-engineered solutions designed to enhance efficiency and ensure utmost reliability in every inspection task.
Each NDT technique serves a unique purpose in the aerospace industry, contributing to the comprehensive safety and reliability of aircraft. Whether it’s detecting subsurface defects, inspecting weld quality, or identifying corrosion, these techniques play a pivotal role in mitigating risks and ensuring compliance with stringent safety standards.
Benefits of NDT in Aerospace
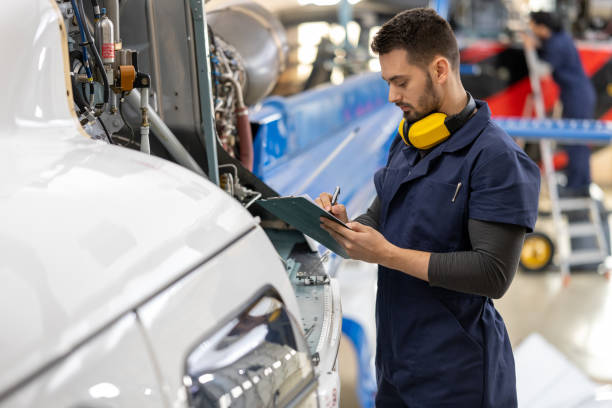
Non-destructive testing plays a critical role in ensuring the safety, reliability, and efficiency of the aerospace industry. The benefits of NDT in the aerospace industry are manifold, encompassing various aspects of aircraft design, manufacturing, maintenance, and operation.
1. Enhanced Safety
NDT techniques enable thorough inspections of aerospace components without causing damage, ensuring that critical parts meet stringent safety standards. By detecting defects and irregularities early on, NDT helps prevent catastrophic failures.
2. Improved Reliability
By detecting hidden flaws and defects, NDT ensures the reliability of aerospace components throughout their operational lifespan. This reduces the risk of unexpected failures and minimises downtime, enhancing aircraft availability and operational efficiency.
3. Cost Savings
Early detection of defects through NDT allows for timely maintenance interventions, reducing the likelihood of costly repairs or replacements. Additionally, NDT helps optimise maintenance schedules, preventing unnecessary downtime and maximising the cost-effectiveness of aerospace operations.
4. Regulatory Compliance
Aerospace regulations mandate rigorous inspection and maintenance standards to ensure aircraft safety and airworthiness. NDT techniques facilitate compliance with these regulations by providing accurate and reliable assessments of critical components, ensuring adherence to industry standards and regulatory requirements.
5. Extended Service Life
By identifying and addressing structural issues early in the aircraft’s lifecycle, NDT contributes to extending the service life of aerospace components. This allows operators to maximize the return on investment in aircraft assets while maintaining optimal safety and performance levels.
6. Quality Assurance
NDT plays a crucial role in quality assurance throughout the aerospace manufacturing process. By verifying the integrity of materials, welds, and assemblies, NDT helps maintain high-quality standards, ensuring that aerospace components meet design specifications and performance requirements.
7. Enhanced Performance
Through the detection of defects such as cracks, voids, or material inconsistencies, NDT contributes to improving the overall performance of aerospace systems. By identifying areas for optimization or structural reinforcement, NDT enables engineers to enhance aircraft efficiency, durability, and aerodynamic performance.
8. Risk Mitigation
By systematically identifying and mitigating potential risks associated with structural defects or material degradation, NDT helps aerospace operators and manufacturers minimise operational risks and liabilities. This proactive approach to risk management ensures the continued safety and reliability of aerospace systems.
9. Innovation and Technology Advancement
The development of advanced NDT techniques and technologies drives innovation and advancement in the aerospace industry. By pushing the boundaries of inspection capabilities, NDT fosters continuous improvement in aircraft design, materials science, and manufacturing processes, paving the way for safer, more efficient aerospace solutions.
10. Environmental Sustainability
Effective maintenance and inspection practices facilitated by NDT contribute to reducing the environmental impact of aerospace operations. By optimising fuel efficiency, minimising emissions, and extending the lifespan of aircraft components, NDT supports sustainable aviation practices and environmental stewardship initiatives.
Real-World Examples
NDT has been instrumental in preventing accidents and ensuring the safety of aircraft in real-world scenarios. From detecting fatigue cracks in turbine blades to identifying corrosion in airframe structures, NDT techniques have saved countless lives and preserved the integrity of aerospace systems. Here are real-world examples illustrating how NDT has prevented accidents and ensured the safety of aircraft.
- Detection of Fatigue Cracks in Turbine Blades:
- Example: During routine maintenance of a commercial airliner, ultrasonic testing detects fatigue cracks in several turbine blades of the jet engine. Prompt replacement of the damaged blades prevents the risk of engine failure during flight, ensuring passenger safety and preventing a potential catastrophic accident.
2. Identification of Corrosion in Airframe Structures:
- Example: During a scheduled inspection of an aircraft’s fuselage using visual and eddy current testing, signs of corrosion are detected in certain structural components. Immediate corrosion treatment and repair are undertaken, preventing structural weaknesses that could compromise the airframe’s integrity and lead to in-flight accidents.
These examples highlight how NDT techniques play a critical role in proactively identifying potential safety hazards, allowing for timely maintenance and interventions to prevent accidents and ensure the safety of both passengers and crew.
Why Safety is Paramount in the Aerospace Industry?
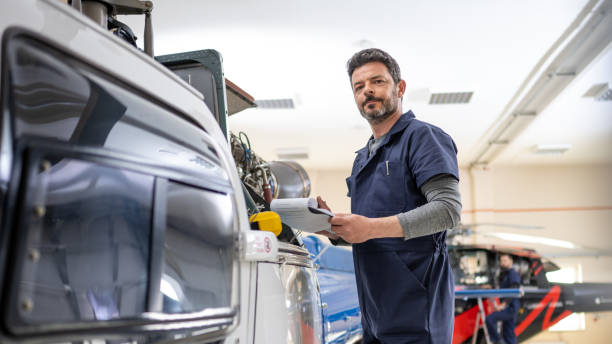
Safety is the bedrock upon which the entire aerospace industry is built. With millions of lives and significant investments at stake, any compromise in safety standards could lead to catastrophic consequences. Hence, stringent measures and advanced technologies are employed to maintain the highest levels of safety and reliability.
It involves rigorous testing, maintenance, and adherence to strict regulations to prevent accidents and ensure smooth operations in the industry. NDT plays a crucial role in ensuring the structural integrity and operational reliability of aircraft.
By employing sophisticated testing methodologies, NDT helps identify defects, flaws, and irregularities in aerospace materials and components without causing any damage. This proactive approach enables timely maintenance and prevents potential failures, thereby upholding safety standards.
Conclusion
NDT solutions play a pivotal role in safeguarding the safety and reliability of the aerospace industry. As the aerospace industry continues to evolve, the importance of NDT in upholding safety standards remains paramount.
With a commitment to innovation and customer satisfaction, NDT Products stands at the forefront of the NDT industry, offering not just products, but the best solutions tailored to meet the unique requirements of each client.