Table of Contents
- History of Eddy-Current Testing
- Types of Flaws Detectable by Eddy Current Testing
- Industries Utilizing Eddy Current Testing
- Eddy Current Testing Procedure
- Eddy Current Testing Equipment
- Advantages of Eddy Current Testing
- Disadvantages of Eddy Current Testing
- Need for Eddy Current Testing Standards and Codes
- Conclusion
Eddy Current Testing is a powerful NDT technique widely used across various industries to detect surface and near-surface flaws in conductive materials. Employing electromagnetic principles, this method has become indispensable in ensuring the integrity and safety of critical components and structures. By inducing electrical currents in the material being tested, eddy current testing can identify cracks, corrosion, and other defects that may compromise the performance of the material. This technique is particularly useful for inspecting components made of metals such as aluminum, copper, and steel.

History of Eddy-Current Testing
The roots of eddy current testing trace back to the late 19th century, when French Physicist, Leon Foucault, first observed eddy currents induced in conductive materials. However, it wasn’t until the mid-20th century that significant advancements were made, leading to the development of modern eddy current testing techniques. Over the years, continuous innovation has refined the process, making it more reliable and efficient.
Types of Flaws Detectable by Eddy Current Testing
Eddy current testing can identify a wide range of flaws, both surface-breaking and sub-surface, including cracks, voids, laps, and inclusions. By analyzing changes in electrical conductivity and magnetic permeability, the technique can pinpoint even minute defects that may compromise structural integrity. These flaws include.
1. Cracks
Eddy current testing can identify cracks on the surface or just below it, irrespective of their size or orientation. This capability makes it invaluable for detecting critical flaws that could lead to catastrophic failure if left undetected.
2. Voids
Voids, or air pockets within the material, can compromise its structural integrity. Eddy current testing can detect voids, ensuring that the material meets quality standards and reducing the risk of failure in service.
3. Laps
Laps occur when there is incomplete fusion between layers of material during manufacturing or Welding Processes. Eddy current testing can identify laps, which can weaken the material and lead to premature failure under stress.
4. Inclusions
Inclusions are foreign particles or impurities embedded within the material. Eddy current testing can detect these inclusions, which may weaken the material or serve as initiation points for cracks.
Industries Utilizing Eddy Current Testing
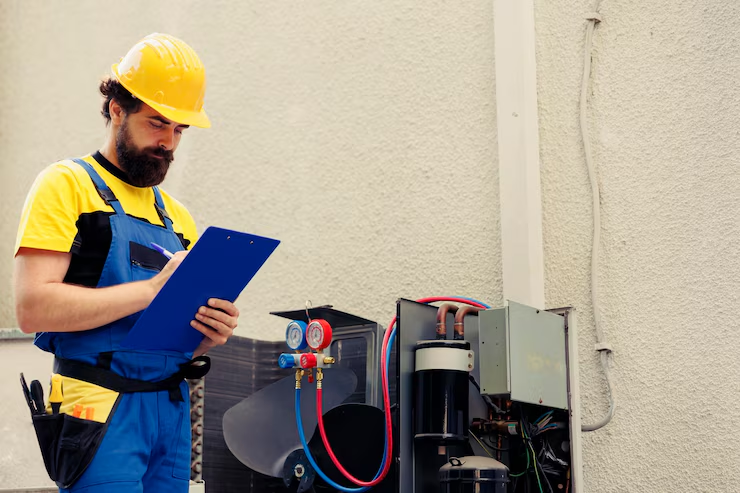
1. Automotive Industry
In the automotive sector, eddy current testing plays a crucial role in ensuring the quality and reliability of critical components such as engine parts, gears, and transmission components. Automated Eddy Current testing can take place at a rapid pace, making it an ideal solution for the high production automotive environment. By conducting thorough inspections, manufacturers can identify defects early in the production process, minimizing the risk of component failure and enhancing overall vehicle performance and safety.
2. Aerospace Industry
The eddy current tester is indispensable in the Aerospace Industry for safeguarding critical aircraft components against flaws that could compromise safety and performance. Components such as turbine blades, landing gear, and structural elements undergo rigorous inspection using eddy current testing to detect surface defects, cracks, and material irregularities. By ensuring the integrity of these components, eddy current testing contributes to the safety and reliability of aircraft operations.
3. Power Generation Sector
Within the power generation sector, eddy current testing is employed to inspect steam turbine generator components for defects. Critical components such as rotor shafts, turbine blades, and generator windings undergo periodic inspections using eddy current testing to detect flaws such as cracks, corrosion, and material degradation. By identifying defects early, power generation facilities can prevent unexpected failures and ensure the continuous and reliable operation of their equipment.
Eddy Current Testing Procedure
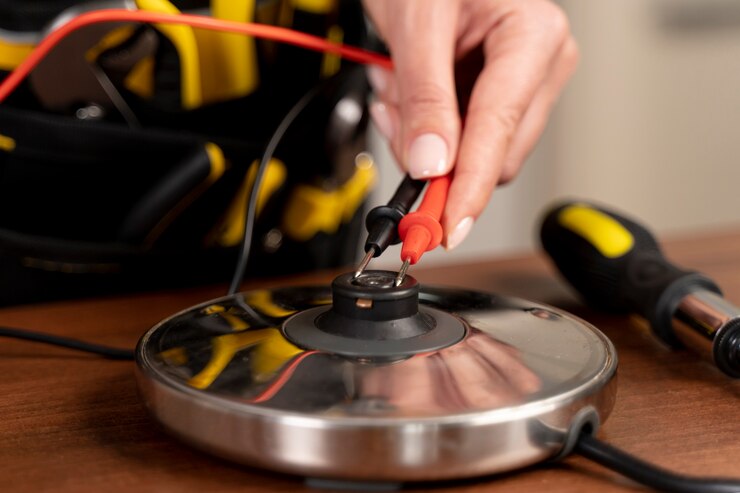
The eddy current testing procedure includes the use of coils or probes to induce eddy currents in the material being tested, which can detect surface cracks or defects. Additionally, the testing process may need to be adjusted based on the specific material properties and thickness being examined. The procedure for eddy current testing involves several key steps.
1. Inducing a Varying Magnetic Field
A varying magnetic field is induced in the material being inspected using a Eddy Current Probe or coil. This magnetic field generates eddy currents within the material, which interact with the material’s properties.
2. Interaction with Material
The induced eddy currents interact with the material, producing signals that contain information about the material’s characteristics and any flaws present.
3. Signal Analysis
The signals produced by the interaction between the eddy currents and the material are analyzed using specialized equipment. Changes in impedance or phase angle are measured, providing insights into the presence and characteristics of flaws within the material.
4. Flaw Detection and Evaluation
By analyzing the signals obtained from the material, defects such as cracks, voids, or inclusions can be identified and evaluated. The size, location, and nature of the flaws are determined, allowing for appropriate action to be taken to address any issues identified.
Eddy Current Testing Equipment
Eddy Current Testing Equipment comprises various components essential for the inspection process. These components include a probe, coil, and impedance analyzer, all of which work together to generate and interpret eddy currents in the material being tested. Additionally, eddy current testing equipment may also include features such as adjustable frequency settings and data recording capabilities for more precise inspections.
1. Probes:
Probes are used to generate the magnetic field and induce eddy currents in the material under inspection. They come in different shapes and sizes to accommodate various applications and geometries of test objects.
2. Coils:
Coils are another type of electromagnetic component used in eddy current testing. They can be either fixed or rotating, depending on the specific requirements of the inspection.
3. Instrumentation:
Advanced instrumentation is used for signal processing and analysis. This includes equipment for real-time data acquisition, signal amplification, filtering, and interpretation. The instrumentation plays a crucial role in enhancing inspection accuracy and efficiency.
4. Data Display and Recording:
The equipment may also include features for displaying and recording inspection data in real-time. This allows inspectors to visualize and analyze the results as the inspection is being conducted, facilitating prompt decision-making and action.
Advantages of Eddy Current Testing
One of the primary advantages of eddy current testing is its non-destructive nature, which allows for thorough inspections without causing damage to the tested material. It offers high sensitivity to surface flaws, making it ideal for detecting minute defects. Furthermore, eddy current testing is relatively fast and can be automated for increased efficiency.
- The non-destructive nature ensures thorough inspections without causing damage to the tested material.
- High sensitivity to surface flaws enables the detection of minute defects.
- A relatively fast inspection process enhances efficiency.
- Automation capability further improves efficiency and throughput.
Trust NDT Products for all your non-destructive testing needs and experience performance and durability with every inspection.
Disadvantages of Eddy Current Testing
Despite its many benefits, eddy current testing does have limitations. It is most effective for surface and near-surface inspections, with limited penetration depth compared to other NDT Methods like radiographic testing. Additionally, the conductivity of the material being tested can affect the accuracy of results, and the equipment setup and interpretation require skilled personnel.
- Limited effectiveness for deep inspections, primarily suitable for surface and near-surface flaws.
- Restricted penetration depth compared to other non-destructive testing methods like Radiographic Testing.
- The accuracy of results may be influenced by the conductivity of the material being tested.
- Skilled personnel are required for equipment setup, operation, and result interpretation.
Need for Eddy Current Testing Standards and Codes
Standardization is pivotal in maintaining the reliability and consistency of eddy current testing outcomes. Across industries, adherence to established international standards and codes is essential for ensuring the quality and regulatory compliance of testing processes. A few reasons are discussed below.
1. Reliability and Consistency:
Standardization ensures that eddy current testing procedures are conducted consistently, regardless of the testing environment or operator. This consistency enhances the reliability of results and facilitates meaningful comparisons between different tests and test locations.
2. Quality Assurance:
By providing guidelines for equipment calibration, inspection procedures, and acceptance criteria, standards and codes help maintain the quality of eddy current testing processes. This, in turn, ensures that the testing outcomes meet the desired quality standards and regulatory requirements.
3. Regulatory Compliance:
In many industries, compliance with specific standards and codes is mandatory to meet regulatory requirements. Adhering to these standards not only ensures the quality of testing but also helps organizations demonstrate compliance with regulatory bodies, thereby avoiding potential legal and financial consequences.
4. Equipment Calibration:
International standards outline the procedures and requirements for calibrating eddy current testing equipment to ensure accurate and reliable measurements. These standards specify calibration methods, frequencies, and acceptable tolerance levels to maintain equipment performance.
Conclusion
Eddy current testing is a versatile and effective non-destructive testing method with widespread applications across industries. Its ability to detect surface and near-surface flaws with high sensitivity makes it invaluable for ensuring the integrity of critical components and structures. Continuous advancements in technology further enhance its capabilities, making it an indispensable tool for quality control and safety assurance. With a commitment to innovation and customer satisfaction, NDT Products stands at the forefront of the NDT industry, offering not just products, but the best solutions tailored to meet the unique requirements of each client.